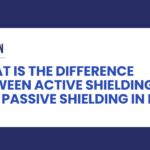
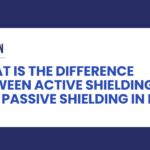
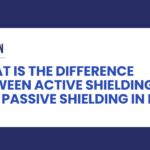
What Is the Difference Between Active Shielding and Passive Shielding in MRI?
July 8, 2025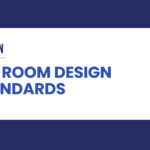
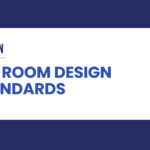
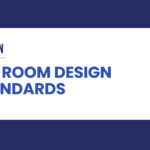
MRI Room Design Standards
July 8, 2025Magnetic Resonance Imaging (MRI) is one of the most advanced diagnostic tools in modern healthcare—but operating an MRI scanner safely requires more than just the equipment itself. The room it occupies must be carefully engineered to control magnetic fields and block external interference. So how are MRI rooms shielded?
MRI shielding is a clinical, operational, and regulatory necessity. It protects scan integrity, ensures compliance with electromagnetic exposure limits, and creates a safe working environment for staff and patients alike.
At Gaven Industries, we specialize in designing and installing MRI shielding systems that integrate seamlessly into hospital infrastructure without compromising performance. To learn more about the science behind shielding, visit our MRI Shielding page. You can also review MRI room shielding requirements for a full breakdown of materials, testing, and code compliance.
How are MRI rooms constructed?
MRI rooms are designed as electromagnetic environments. They must contain both radiofrequency (RF) signals and static magnetic fields while allowing for mechanical, electrical, and clinical functionality. Shielding systems are therefore embedded directly into the architectural structure of the suite—beneath finishes, behind walls, and around every penetration.
Key components of MRI room construction include:
- RF shielding systems: Gaven uses soldered copper or galvanized steel panels to form a continuous Faraday cage. These panels are engineered to meet IEEE-299 and MIL-STD-285 testing requirements, blocking RF signals from entering or exiting the room.
- Magnetic shielding: Passive magnetic shielding is built into walls, floors, or ceilings using silicon steel or mu-metal to redirect fringe fields and preserve the 5 Gauss zone. This is critical when MRI suites are located near elevators, critical care spaces, or power infrastructure.
- HVAC and utility integration: Every air duct, gas line, and cable pass-through must be shielded using RF waveguides and filters to preserve attenuation integrity.
- Non-magnetic construction materials: Every interior finish—from framing and fasteners to fixtures and furniture—is specified as MRI-safe to prevent ferromagnetic attraction or interference with scan performance.
At Gaven, we design MRI shielding systems using proprietary modeling tools that simulate magnetic flux and RF leakage—so performance is engineered, not assumed.
Why is there no metal in an MRI room?
Ferromagnetic metals pose serious safety hazards in MRI environments. Even small items can become lethal projectiles if introduced into the magnet room. Beyond safety, metal can distort the magnetic field and compromise image quality.
Common risks include:
- Projectile incidents: Unsecured objects are rapidly accelerated into the magnet bore, endangering patients and staff.
- Image degradation: Metal can cause signal voids, warping, or ghosting—affecting scan readability and clinical accuracy.
- Burn risks: Conductive materials can act as antennas during scanning, heating up and causing patient burns or equipment failure.
That’s why MRI shielding companies like Gaven Industries implement strict material controls during construction. Every screw, bracket, and cable tie used inside the scan room is vetted for non-ferrous composition. Our construction crews are trained in MRI-safe protocols, reducing risk at every phase of the build.
What are MRI rooms lined with?
MRI rooms are lined with conductive shielding materials that block unwanted RF signals and, when needed, contain magnetic fringe fields. This lining forms a continuous, grounded barrier—completely enclosing the room and turning it into a shielded enclosure.
Common MRI room shielding materials include:
- Soldered copper panel systems: Gaven’s flagship RF solution, engineered for maximum shielding effectiveness, electrical continuity, and long-term corrosion resistance.
- Galvanized steel panel systems: Ideal for hybrid environments where value engineering or dual-purpose shielding is required.
- Mu-metal and silicon steel: Used for fringe field mitigation where the static magnetic field needs to be shaped or blocked from reaching adjacent rooms or sensitive infrastructure.
Every seam, joint, and connection is tested for electrical continuity. Every penetration—HVAC duct, medical gas line, power conduit—is sealed with a waveguide or RF filter. This meticulous integration ensures that shielding performance is not compromised by construction shortcuts.
Why are MRI rooms lined with copper?
Copper is the gold standard for RF shielding in MRI environments due to its unparalleled electrical conductivity and shielding effectiveness. It blocks both high- and low-frequency interference across the RF spectrum and offers exceptional durability in clinical environments.
Copper is used in several configurations:
- Soldered solid panels: Gaven’s preferred approach for premium builds, offering unmatched shielding continuity and longevity.
- Modular panel systems: Pre-fabricated for faster deployment and precision fit, especially in new build scenarios.
- Copper waveguides and filters: Integrated into every passthrough—ensuring airflow, power, and data access without breaking the shield.
All copper systems installed by Gaven Industries are tested for grounding, attenuation, and electrical bonding. Our RF filters for MRI rooms meet or exceed all OEM specs and integrate seamlessly into both new construction and renovation projects.
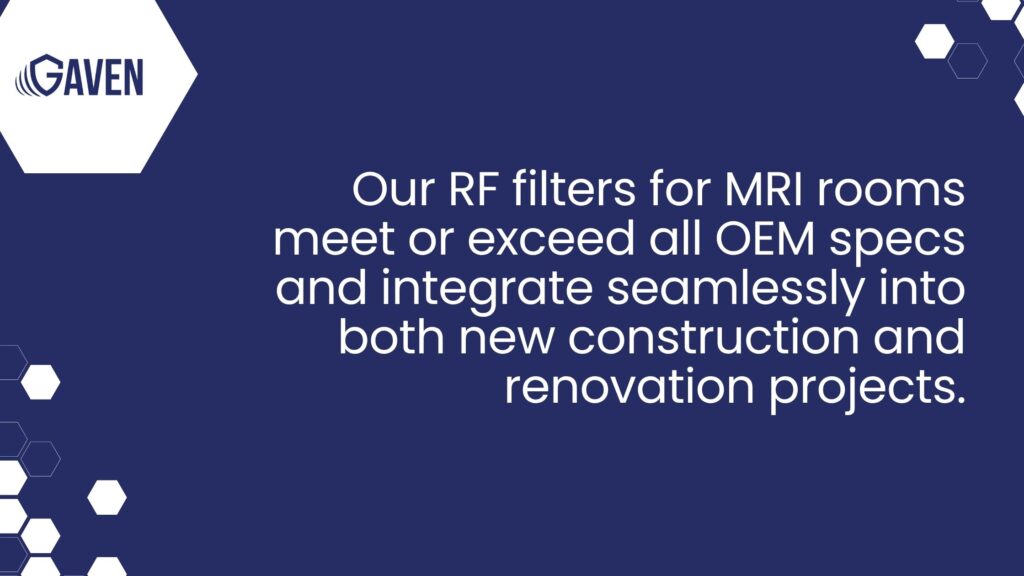
Build your MRI room with confidence
MRI room shielding isn’t a line item—it’s the backbone of the suite’s functionality. It determines whether images are usable, whether patients are safe, and whether the room passes inspection or fails pre-test certification.
Looking to meet strict MRI room shielding requirements with the most reliable materials? Gaven Industries offers full-spectrum solutions backed by decades of expertise in MRI Shielding. We’re one of the few MRI shielding companies that design, fabricate, install, and test our own systems—ensuring compliance from blueprint to final scan.
Let’s build it right, the first time.