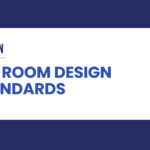
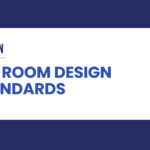
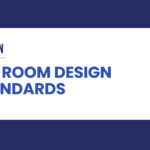
MRI Room Design Standards
July 8, 2025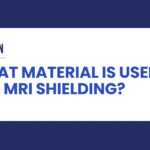
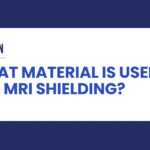
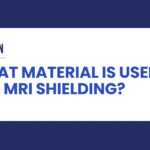
What Material Is Used for MRI Shielding?
July 8, 2025MRI rooms aren’t built like ordinary clinical spaces—and for good reason. Every MRI scanner generates powerful static and radiofrequency (RF) fields that can disrupt nearby equipment, pose safety risks, and interfere with scan results. To keep these forces contained, MRI suites are lined with specialized metallic shielding.
But not just any metal will do.
The metals used in shielding systems must meet exacting standards of conductivity, permeability, and structural integration. And choosing the wrong material—or installing it incorrectly—can lead to scan artifacts, compliance failures, or safety hazards.
This guide breaks down what metallic shielding is used in MRI rooms and why material selection matters more than most people realize.
To understand how these materials fit into the broader system, visit our MRI Shielding page. You can also explore our deep dive on MRI shielding companies to learn how real-world experience shapes design and execution.
What is the purpose of shielding in an MRI suite?
MRI shielding isn’t optional—it’s essential infrastructure.
The moment a superconducting magnet is energized, it creates a static magnetic field that extends well beyond the scanner. Combine that with RF signals used during imaging, and you have a complex electromagnetic environment that requires active control.
Shielding serves three primary purposes:
- Keeps unwanted RF interference out
- Prevents magnetic fringe fields from affecting adjacent areas
- Protects staff and patients from unsafe exposure to ferromagnetic forces
The key is containment—not just physically, but electromagnetically. At Gaven, we use performance modeling and OEM specs to ensure each shielding design aligns with magnetic shielding theory, clinical performance requirements, and building code mandates.
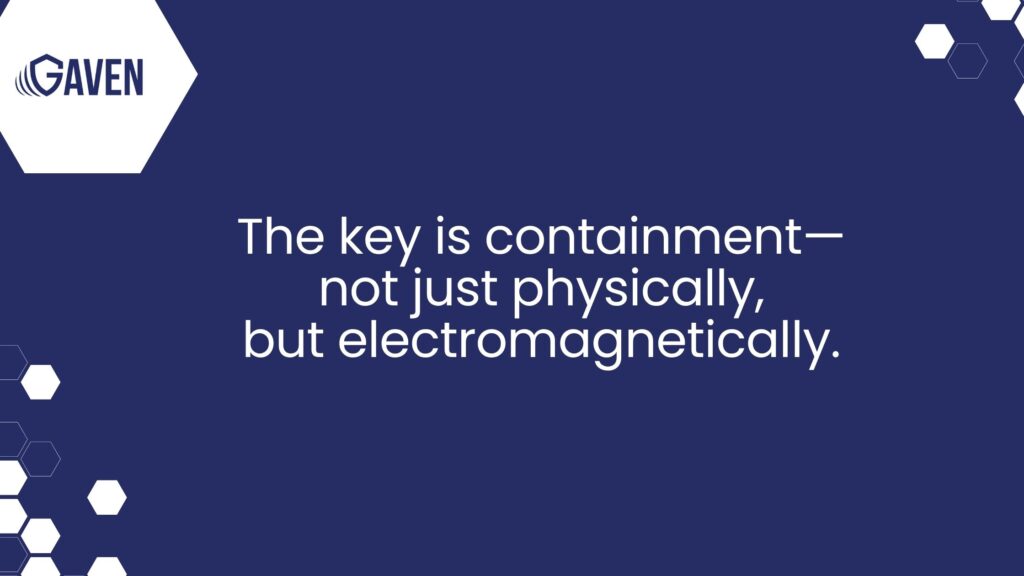
What is the best metal to block radio waves?
There’s a reason copper is the go-to for RF shielding. With exceptional conductivity and long-term stability, it forms the backbone of most Faraday cage systems used in MRI suites.
Still, copper isn’t the only option:
- Galvanized steel provides decent attenuation at a lower cost and doubles as a structural surface.
- Aluminum is lightweight but less conductive—generally reserved for non-clinical environments or budget-sensitive projects.
Each material choice reflects a balance of:
- Conductivity
- Corrosion resistance
- Project constraints
Here’s a quick side-by-side comparison of the most common RF shielding materials:
Material | Conductivity | Corrosion Resistance | Cost | Clinical Preference |
Copper | Excellent | Excellent | $$$ | High |
Galvanized Steel | Good | Good | $$ | Medium |
Aluminum | Fair | Fair | $ | Low (for MRI) |
“Copper will always outperform, but it’s not just about the metal—it’s about how it’s sealed, bonded, and integrated into the system.”
— John J. Gaviglia, Founder, Gaven Industries
What is the common metal used as a shielding device?
Let’s separate RF shielding from magnetic shielding.
When it comes to RF:
- Copper mesh or sheeting is the standard.
- Joints are soldered, not taped.
- Seams are sealed.
- The enclosure is grounded to a single point to form a true Faraday cage.
For magnetic shielding:
- Steel plates are embedded in wall or floor assemblies to redirect fringe fields.
- Mu-metal, an ultra-high-permeability alloy, is used in critical zones or when fringe fields must be tightly controlled.
These materials serve different purposes—but both are essential to MRI suite integrity. One manages electromagnetic isolation; the other handles spatial field control.
What metallic shielding is used in MRI rooms?
So what does a complete MRI room shielding system actually look like?
You’re likely to find:
- Copper RF panels lining the room’s walls, ceiling, and floor—pre-fabricated and field-soldered for a seamless shield
- Galvanized steel used for hybrid shielding or where budget and strength are both priorities
- Mu-metal inserts strategically placed to contain fringe fields around elevators, data rooms, or ORs
These components are installed behind finished surfaces, coordinated with electrical, mechanical, and architectural elements. Every passthrough—whether for HVAC, lighting, gas, or conduit—must be waveguided or filtered to maintain continuity.
MRI shielding companies like Gaven handle this integration end to end, from design to certification. We test each system to IEEE-299 and MIL-STD-285 standards and provide attenuation documentation that satisfies OEMs, inspectors, and regulatory agencies alike.
Metal is the medium—but performance is the goal
It’s easy to focus on materials, but effective shielding goes far beyond product selection. The real differentiators are:
- System integration
- Installation precision
- Field validation
Even the best copper will fail if a filter is installed improperly, a seam is missed, or a penetration is left unshielded. That’s why Gaven Industries takes a “no assumptions” approach—modeling every room, building every panel in-house, and overseeing installation through certified technicians.
“Shielding is invisible when done right. You don’t see it—you see the image clarity, the patient safety, the regulatory sign-off. That’s the product.”
— John J. Gaviglia, Founder, Gaven Industries
Choosing the right metallic RF shielding and magnetic shielding material is critical to MRI safety and performance. Partner with Gaven Industries, one of the most trusted MRI shielding companies, to ensure your facility is fully protected and compliant with modern MRI Shielding standards.